وبلاگ
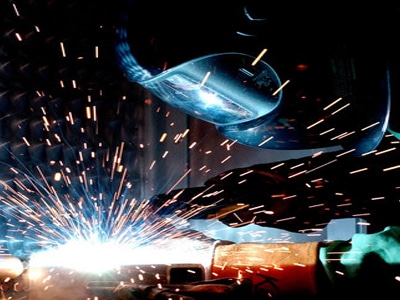
انتخاب فرآیند جوشکاری مناسب
در بسیاری موارد اتصال طراحی شده را میتوان با چند فرآیند جوشکاری مختلف ایجاد نمود. اما همواره یک فرآیند است که بهترین نتیجه را (در مجموع) ایجاد میکند. بنابراین یک متخصص جوش باید بتواند با روشی مقبول٫ یکی از فرآیندهای ممکن را برای اتصال مورد نظر تعیین نماید. در این متن شما با روال انتخاب فرآیند جوشکاری مناسب آشنا میشوید. این روال شامل ۴ مرحله میگردد:
مرحله اول:
بررسی ویژگیهای مورد نیاز اتصال
در این مرحله باید بزرگ یا کوچک بودن اتصال جوش٫ موقعیت و جهت جوشکاری٫ و ضخامت فلز پایه باید بررسی گردد.
در جوشکاری٫ ملزومات هر اتصالی را میتوان در ۴ ویژگی خلاصه کرد: پرکنندگی سریع(نرخ رسوب بالا)٫ انجماد سریع (در موقعیتهای دشوار جوشکاری)٫ سرعت جوشکاری زیاد (سرعت حرکت قوس بالا و بستر جوش بسیار کوچک)٫ و نفوذ (عمق نفوذ جوش در فلز پایه).
پرکنندگی سریع هنگامی نیاز است که به مقدار زیادی فلز جوش برای پر کردن اتصال احتیاج باشد. بستر جوشهای بزرگ را تنها میتوان با نرخ رسوب بالا٫ در زمان کم ایجاد کرد. در بستر جوشهای کوچک٫ پرکنندگی سریع یک پارامتر فرعی میباشد.
انجماد سریع در جوشکاری موقعیتهای دشوار (بالا سری و عمودی) مد نظر قرار میگیرد که نیاز است حوضچه مذاب جوش خیلی سریع منجمد گردد.
سرعت جوشکاری بالا به معنی پیشروی سریع قوس و فلز مذاب و ایجاد یک بستر جوش پیوسته و مناسب بدون انقطاع و بریدگی میباشد. این خصوصیت در جوشهای تک پاسه کوچک٫ مانند جوشکاری ورقها٫ مد نظر است.
نفوذ با نوع اتصال تغییر میابد. در بعضی اتصالات نفوذ باید عمیق باشد تا به مقدار کافی از فلز پایه با فلز جوش ترکیب شود و در برخی دیگر باید نفوذ محدود شود تا از سوختگی و ترک جلوگیری گردد.
مرحله دوم:
تطبیق ویژگیهای مورد نیاز اتصال با فرآیندهای جوشکاری.
اغلب سازندگان دستگاه های جوش اطلاعات مختلفی را در ارتباط با ویژگیها و توانایی دستگاه های خود ارائه میدهند که میتوان از آنها استفاده نمود. در این مرحله با توجه به خصوصیات هر دستگاه و ویژگیهای هر فرآیند میتوان یک یا چند فرآیند را به گونه ای انتخاب کرد که خصوصیات تعیین شده برای اتصال را فراهم سازد. در این حالت بندرت پیش میاید که تنها یک فرآیند انتخاب شود و معمولا دو یا چند فرآیند خصوصیات مد نظر را تامین میکنند.
مرحله سوم:
تهیه چک لیستی برای تعیین توانایی فرآیندهای انتخاب شده در تطبیق با شرایط خاص کاری.
پارامترهای دیگری نیز علاوه بر اتصال روی انتخاب فرآیند تاثیر میگذارند. بسیاری از آنها مختص شرایط کار و کارگاه جوشکاری شما میباشند. گاهی این پارامترها تاثیر زیادی بر حذف برخی فرآیندهای انتخاب شده دارند. در این مرحله باید تمامی این پارامترها را بصورت چک لیست درآورده و یکی یکی بررسی نمود.
حجم تولید:
باید هزینه دستگاه جوش را با مقدار کار یا تولید مورد نیاز تطبیق داد. اگر حجم کار برای یک کاربرد باندازه کافی نباشد٫ میتوان کاربرد دیگری را نیز بطور موازی در نظر گرفت تا هزینه ها تعدیل گردد.
خصوصیات جوش:
در صورتیکه یک فرآیند نتواند خواص جوش تعیین شده را تامین نماید٫ از لیست انتخابها حذف میگردد.
مهارت کاربر:
کاربران ممکن است که مهارت کار با یک فرآیند را خیلی سریعتر از فرآیندهای دیگر کسب نماید. آموزش کاربران برای یک فرآیند جدید هزینه ساز است.
تجهیزات کمکی:
هر فرآیند دارای منبع تغذیه و تجهیزات کمکی خاص خود میباشد. اگر یک فرآیند را بتوان با تجهیزات موجو اجرا نمود٫ هزینه اولیه بسیار کاهش میابد.
تجهیزات جانبی:
قابلیت دسترسی و هزینه تجهیزات جانبی مورد نیاز باید مد نظر قرار گیرد.
شرایط فلز پایه:
زنگار٫ روغن٫ لبه سازی٫ جوشپذیری و سایر شرایط فلز پایه باید مد نظر قرار گیرد. این پارامترها میتوانند قابلیت یک فرآیند را محدود نمایند.
وضعیت قوس:
در صورتیکه درز اتصال نامنظم باشد استفاده از فرآیندهای با قوس آزاد ترجیح داده میشود. اما در مواردیکه بتوان درز جوش را بطور مناسبی قرار داد استفاده از فرآیند زیرپودری ارجح است.
قید و بست:
در برخی فرآیندها (بخصوص فرآیندهای نیمه خودکار) نیاز به قید و بست های خاص است که باید مد نظر قرار گیرد.
تنگناهای تولیدی:
اگر فرآیندی هزینه تولید را کاهش دهد اما محدودیتها و مشکلاتی برای تولید ایجاد نماید٫ ارزش خود را از دست میدهد. دستگاه های بسیار پیچیده که نیاز به سرویسکاری مداوم توسط افراد ماهر دارند میتوانند باعث کاهش سرعت تولید شوند.
چک لیست تهیه شده باید تمامی فاکتورهای موثر بر اقتصاد تولید را در بر داشته باشد. فاکتورهای دیگری که میتوان اشاره کرد عبارتند از:
ـ ملزومات تولید
ـ محدوده ابعادی جوش
ـ انعطاف پذیری در کاربرد
ـ طول درز جوش
ـ زمان تنظیم و راه اندازی
ـ هزینه اولیه
ـ ملزومات بهداشتی و زیست محیطی
با تعیین این فاکتورها میتوان فرآیند مناسب را از بین فرآیندهای انتخاب شده تعیین نمود. در صورتیکه تمامی شرایط یکسان باشد٫ معیار انتخای هزینه کلی خواهد بود.
مرحله چهارم:
بازنگری فرآیند با اطلاعات سازنده دستگاه جوش برای تایید توانایی آن.
در این مرحله باید چک لیست تهیه شده و ویژگیهای مورد نیاز با نماینده سازنده دستگاه جوش مورد بازنگری قرار گیرد تا از توانایی دستگاه و انتخاب صحیح اطمینان حاصل شود.